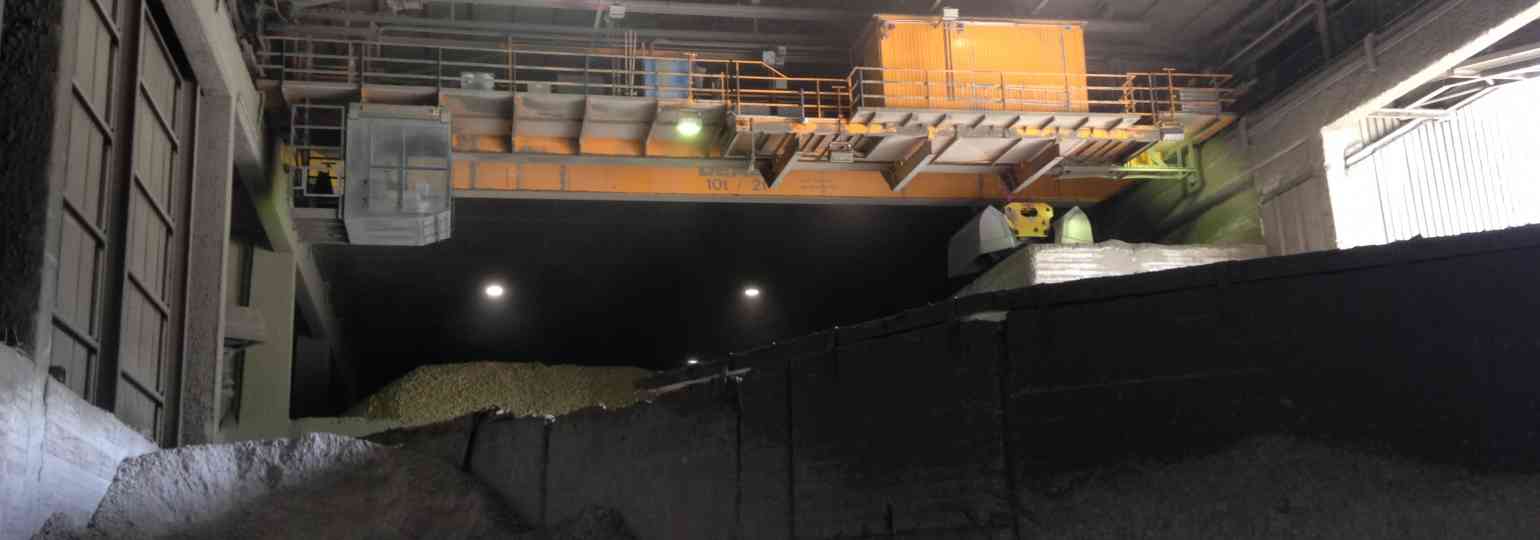
A cement plant’s overhead crane was showing signs of premature fatigue. To curb its accelerated deterioration, reinforcement actions were performed on the equipment. The OSMOS Group was tasked with monitoring changes in the crane’s mechanical behavior, as well as the effects of operating cycles on its condition. By anticipating any deviations, the operator is able to carry out the necessary actions to ensure its structural integrity and personal safety.
Since 2018, the overhead crane has been the subject of structural monitoring, which has detected multiple anomalies, making it possible to anticipate situations before the structure of the equipment and its operation became problematic. The monitoring set-up, comprising eight Optical Strands (long-base extensometers), four short-base extensometers and one temperature sensor, continuously monitors the behavior of the structure. The system is also configured to notify the operator and OSMOS of any anomalies detected in the equipment, in real time.
Thanks to OSMOS’s services, the operator can check and preserve its industrial assets
Faced with shrinking budgets and rising performance demands, keeping equipment in good working order and controlling structural risks, while saving money on maintenance, has become a major concern for industrial plant managers. Within this context, structural health monitoring (SHM) tools have emerged as a solution capable of preventing hazardous situations, but also optimizing control and maintenance costs for civil engineering works and industrial equipment.
Whether the need relates to production line supports, intra- or inter-unit structures, storage facilities, or factories or other industrial buildings, OSMOS solutions contribute real added value to structural monitoring policies. By combining monitoring and behavioral engineering, a structure’s exact state of health can now be determined, namely including any emerging problems and their evolution over time, and the impact of operations on its behavior can also be tracked. Over time, continuous, real-time monitoring makes it possible to adapt the usage and optimize the maintenance of structures based on their health, control personal and property safety, and extend the lifespans of industrial facilities.
More than satisfactory results have prevented critical situations and saved money on maintenance
By placing the overhead crane under continuous monitoring, for a variety of criteria (such as strain cycle counts, vibration frequency and intensity, and static measurements), OSMOS has been able to assess how the structure responds to its operating cycles. After the first analyses, alert thresholds were defined for reporting any noteworthy changes in mechanical behavior. With this ability to be notified instantaneously of any anomalies detected in the structure, the cement plant’s operator is able to guarantee maximum safety for the teams working on site.
In particular, an analysis of deformation cycles identified the appearance of faults in bolted connections, on multiple occasions. The above graph depicts one of the breaks in a single bolt in one of those connections, which occurred on February 16, 2019 (shown in red), and which was foreseen, despite the fact that the bolt had simply come loose, with no visually apparent problems. Once the repair was performed on February 28, 2019, OSMOS’s teams observed an immediate effect on the data, which returned to normal. The discovery of defects in the connections has prevented critical situations that would have led to shutdowns of operations and had serious consequences on employee safety.
Thanks to the monitoring provided by OSMOS, the plant’s operator has an accurate view of the overhead crane’s state of health and its evolution over time. By identifying weaknesses in the equipment, the operator was able to define a new, tailored maintenance schedule and review its priorities, in order to significantly reduce the cost of upkeep. Since June 2020, fewer stresses have observed on the overhead crane. This phenomenon is a direct result of the maintenance actions performed on the equipment and of the optimization of its use.